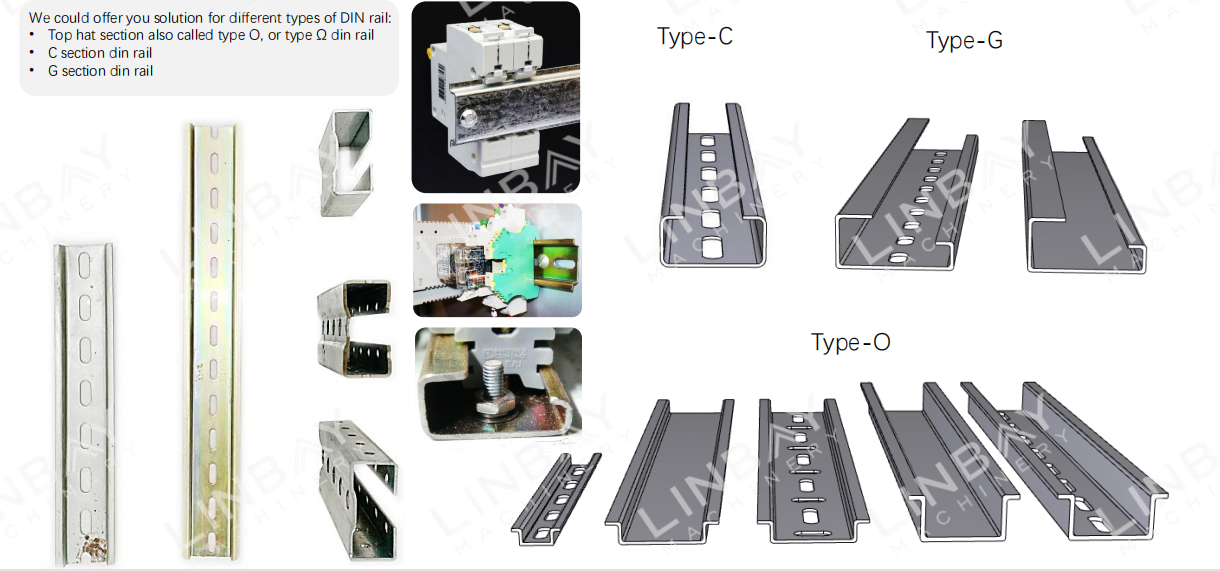
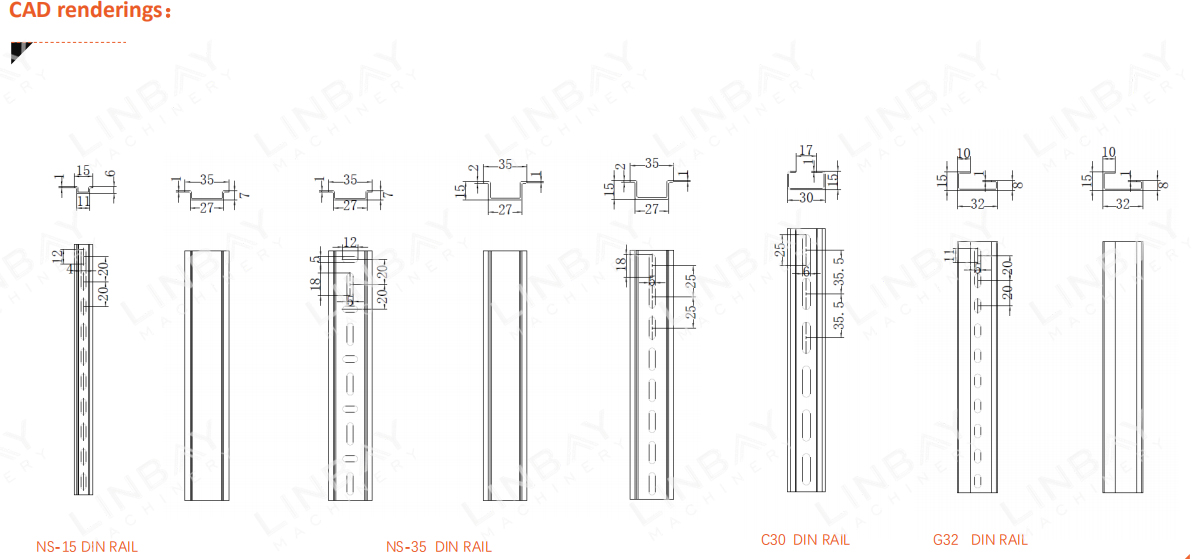

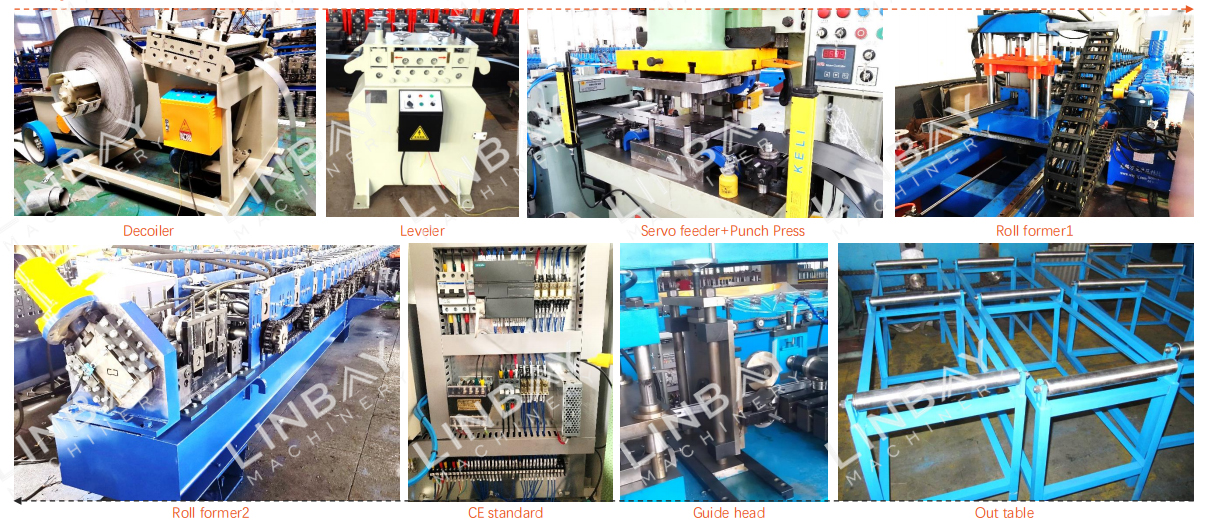
DIN Rail Roll Forming Machine | ||
Item | Specifications | Optional performance |
Machinable Material : | A) Zinc-plated steel | Thickness(MM): 1-1.5 |
B) Aluminum | ||
C) Stainless steel | ||
Yield strength : | 250 - 550 Mpa | |
Tensil stress : | G250 Mpa-G550 Mpa | |
Decoiler : | Manual decoiler | * Hydraulic decoiler (Optional) |
Punching system : | Hydraulic punching station | * Punching press (Optional) |
Forming station : | 10 stands | * According to your profile drawings |
Main machine motor brand : | Shanghai Dedong (Sino-Germany Brand) | * Siemens (Optional) |
Driving system : | Chain drive | * Gearbox drive (Optional) |
Machine structure: | Wall panel station | * Cast Iron (Optional) |
Forming speed: | 10-20 (M/MIN) | * Or according to your profile drawings |
Rollers’ material : | Steel #45 | * GCr 15 (Optional) |
Cutting system : | Post-cutting | * Pre-cutting (Optional) |
Frequency changer brand : | Yaskawa | * Siemens (Optional) |
PLC brand : | Panasonic | * Siemens (Optional) |
Power supply : | 380V 50Hz 3ph | * Or according to your requirment |
Machine color : | Industrial blue | * Or according to your requirment |
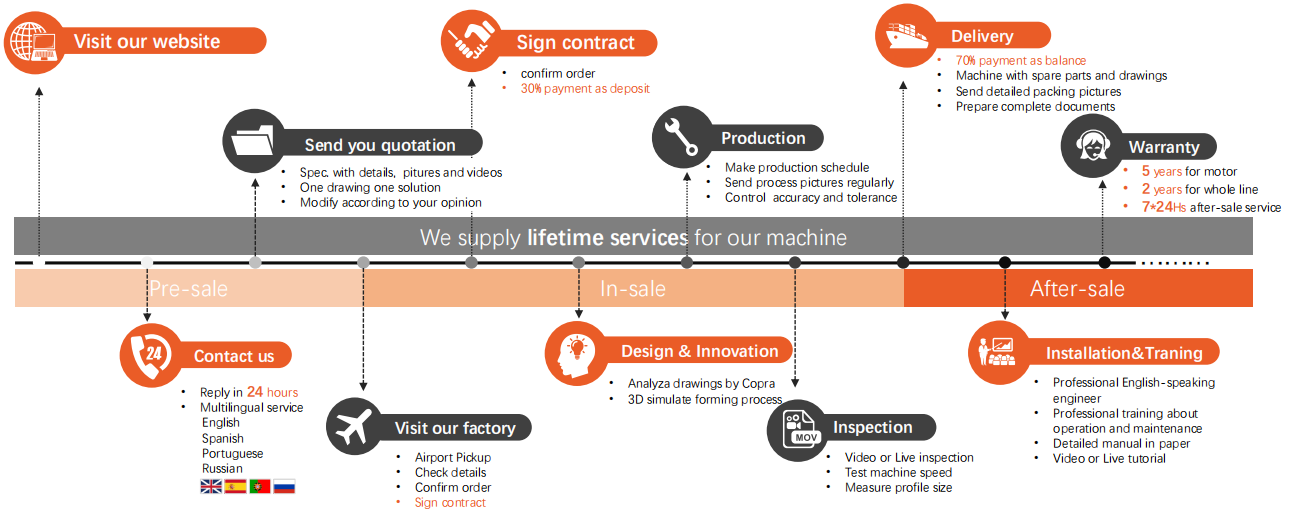