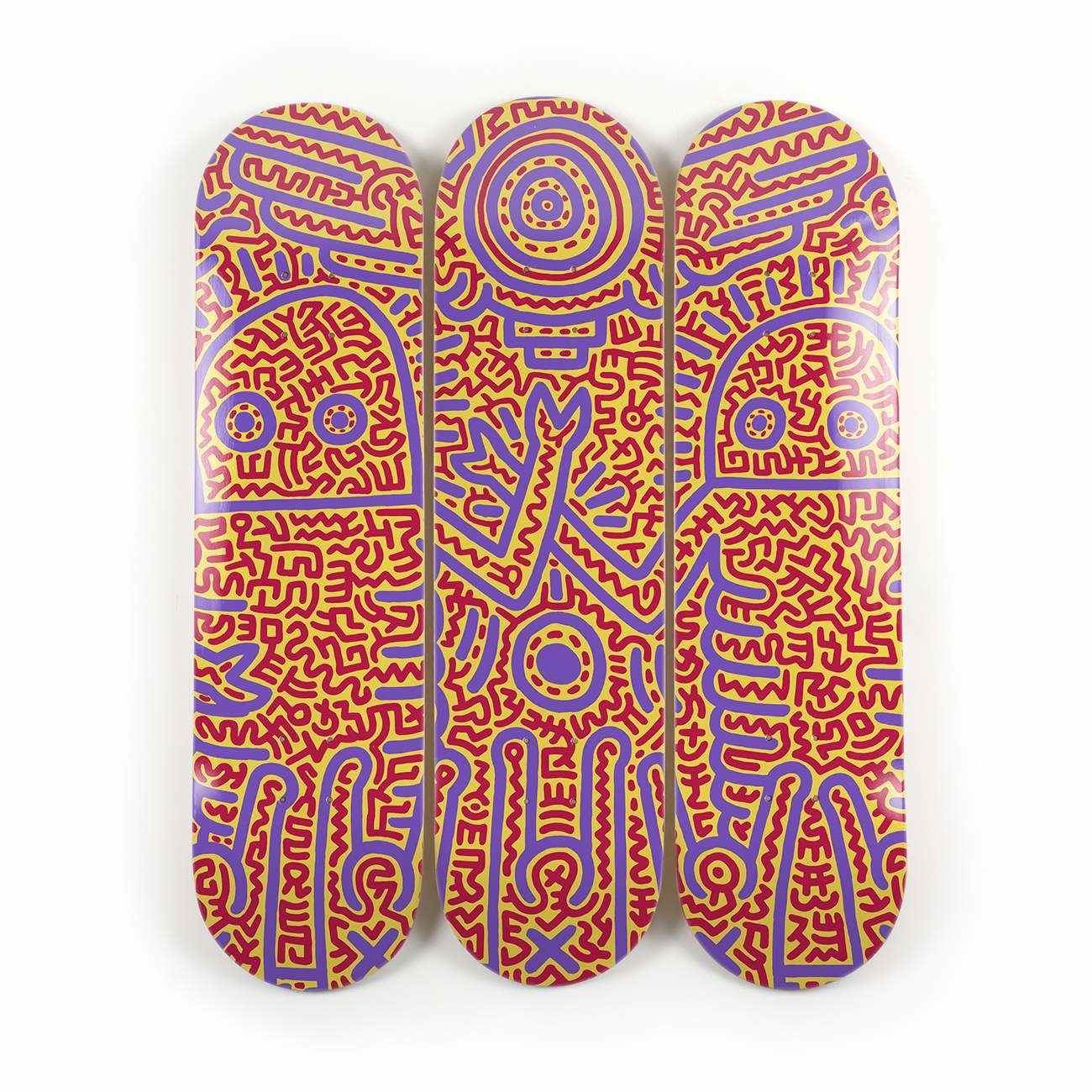
article on the manufacturing process of a roll forming machine and its importance in the construction industry.
Wuxi Linbay Machinery Co., Ltd. is a manufacturer of high-end roll forming machines in China. Their products include roofing roll forming machines, glazed tile roll forming machines, C/Z purline roll forming machines, deck floor roll forming machines, guardrail roll forming machines, cable tray roll forming machines, among others. The company's commitment to creating quality machines has earned them a reputation as one of the best roll forming machinery manufacturers in China.
Roll forming is a manufacturing process that involves shaping a continuous strip of sheet metal or coiled steel into a desired cross-section profile. The process is done by passing the metal through a series of rolls that gradually bend the metal into the desired shape. Roll forming machines are used extensively in the construction industry to create strong, lightweight, and durable building materials.
One of the most important aspects of the roll forming process is profile design. The profile design determines the shape of the finished product and its functionality. To ensure that the profile design is perfect, engineers use Computer-Aided Design (CAD) software to create a 3D model of the desired shape. The design is then sent to the roll forming machine, where the tooling and rolls are manufactured to match the profile.
The next step in the process is material preparation. The raw material, usually in the form of a coil, is fed into the roll forming machine. The machine uncoils the metal strip and feeds it through a series of rollers that gradually bend the metal into the desired shape. The rollers are set up in a line, with each roller performing a specific task. Some rollers are used to bend the metal, while others are used to stretch it or compress it.
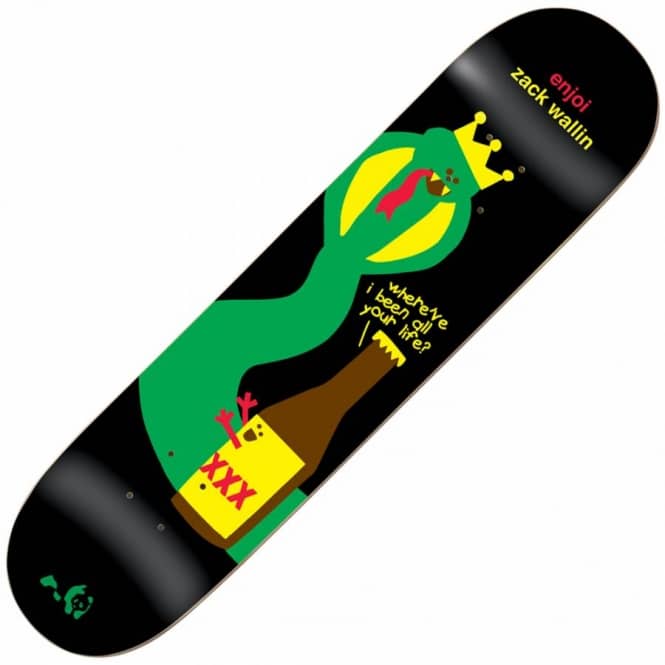
Once the metal has been shaped into the desired profile, it is cut to the desired length. The cut-off shear blade is located at the end of the roll forming machine, and it is used to cut the finished product to the required length. The length of the product is measured using a length encoder, which controls the cut-off shear blade.
The finished product is then inspected for quality. Roll forming machines have sensors and gauges that check the dimensions and quality of the finished product. Any defects or abnormalities are automatically detected and the machine stops. This ensures that only high-quality products are manufactured.
Roll forming machines play an essential role in the construction industry. They are used to create roofing sheets, wall panels, ceiling panels, flooring, and so on. The process is fast, efficient, and cost-effective. The finished products are durable and resistant to harsh weather conditions, making them ideal for construction in different environments.
One of the biggest advantages of using roll forming machines is that they can create complex shapes with a single machine. This means that architects and builders have more design options, and can create unique and innovative structures. Moreover, roll forming machines can produce large quantities of products in a short period. This is particularly useful for construction projects that require a significant amount of material.
In conclusion, roll forming machines are a vital part of the construction industry. They have revolutionized the way that building materials are produced, making the process faster, more efficient, and cost-effective. Wuxi Linbay Machinery Co., Ltd. is one of the leading manufacturers of roll forming machines in China, and their commitment to quality has earned them the trust and respect of their customers. With their state-of-the-art machines and experienced team of engineers, they are poised to lead the way in the roll forming industry for years to come.