All-in-one roll formers
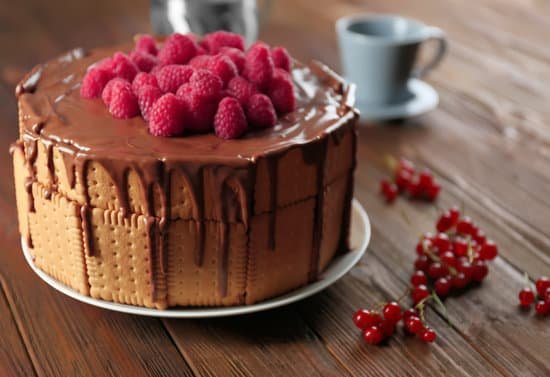
All-in-one roll formers, as the name suggests, can perform multiple functions in one machine. They are designed to create different profiles and shapes in various thicknesses, making them extremely versatile. All-in-one machines can handle both single and double layers of material, which means they can be used for a range of products, including roofing, wall panels, and other industrial applications.
Pros
One of the biggest advantages of an all-in-one machine is its versatility. Manufacturers can use the machine for different products, which means they don’t need to invest in multiple machines. This saves space, money, and time. Additionally, all-in-one machines are easier to set up, operate, and maintain than a range of separate machines.
Cons
The only drawback of all-in-one machines is that they can be more expensive than separate machines. This is because all the functionality is combined into one machine, which can drive the cost up. However, if a manufacturer uses the machine for different applications, the additional cost can be offset by the savings in not buying multiple machines.
Multiple single layer roll formers
Multiple single layer roll formers are used for one specific application, shape, or profile. They are designed to only work with a single layer of material and create one specific product. Manufacturers can use the machines for different products, but they need to invest in separate machines.
Pros
One of the biggest advantages of multiple single layer roll formers is the lower initial cost. They are cheaper than all-in-one machines, and they still provide high-quality results. Manufacturers can choose the exact machine they need for their product and budget. Additionally, if one machine breaks down, the production won’t come to a complete stop, as there are other machines to fall back on.
Cons
The biggest drawback of multiple single layer roll formers is that they are inflexible. They can only create one specific shape or profile, and manufacturers need to invest in multiple machines to create different products. This takes up more space, requires more maintenance, and can be time-consuming. Additionally, if a manufacturer doesn’t have a constant need for a specific product, the machine may not be cost-effective.
Conclusion
So, which option is better – an all-in-one double layer roll forming machine or multiple single layer roll formers? It depends on the manufacturer’s needs. If a manufacturer has a constant need for a range of shapes and profiles, an all-in-one machine may be the best choice. However, if a manufacturer only needs to create one specific product, a single layer roll former might be a better option. Ultimately, it comes down to what the manufacturer needs in terms of flexibility, initial cost, maintenance, and production output.
Keywords: Double Layer Forming Machine, All-in-one roll formers, Multiple single layer roll formers, Roll forming industry, Manufacturing.